Four-Ball Wear Test Machine
What is it?
The Four Ball machine provides an evaluation of the anti-wear and extreme pressure properties of fluid lubricants and greases in sliding contacts.
Why do we use it?
This machine is broadly used, mainly to demonstrate performance within industrial applications like greases. The ASTM standard tests are well known in the industry and used as a reference by many lubricant formulators.
How does it work?
A ball, mounted in a chuck, is rotated against three stationary balls in a pot containing the sample lubricant.
MRS-10A Computer Control Four Ball Friction Testing Machine is used to evaluate the loading capacity of lubricants in the process of sliding friction on a constant point under high pressure. The above-mentioned capacity includes: Maximum load PB under unstuck condition, sintered load PD & comprehensive wearing parameter ZMZ. The machine can carry on abrasive wearing test for a long time to test the friction force and obtain the friction co-efficient of the materials. Equipped with special accessories, it can perform end-face friction test and analogue wearing test of materials. Connected with recorder, it can print the curves of Temperature-Time and Friction Force-Time. Equipped with special device, it can display, test and record the test results of grading crack of friction-pair through computer
Main technical parameters:
1 testing force range (stepless adjustable) 60N~10kN
2 the relative error of the test force ± 1%
3 friction test range 0~300N
4 friction test error ± 3%
5 spindle speed range (stepless adjustable) 200~2000r/min
6 spindle speed error ± 5 r/min
7 friction temperature control range room temperature ~75○C
8 friction pair temperature control error ± 2○C
9 test time control range 1 sec ~999 hours
10 spindle speed control range 1~99999999 rpm
A steel ball test forφ12.7mm 11
12 dimension 1200*870*1700 (mm)
13 weight 600kg
using two ASTM test methods, the 4-Ball EP Tester and 4 Ball Wear. The 4 Ball EP Tester focuses on Extreme pressure (EP) properties and the 4 Ball Wear focuses on wear scar (WS), and coefficient of friction (COF)
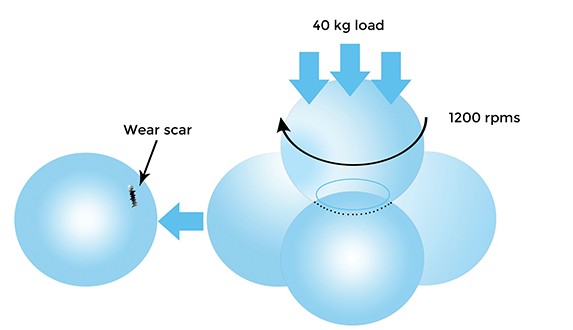
The measurement of Extreme-Pressure properties of a lubricating grease using the 4 Ball method is designated under the ASTM-D 2596. The purpose of this testing is to determine the load carrying capabilities of a lubricating grease under high load applications.
The 4 Ball EP test machine operates in a sliding or rolling motion. A single stainless steel ball rotates onto three stainless balls, all of which are completely coated with a lubricant film, or “boundary”, held stationary in the form of a cradle.
The ability of a grease to perform under extreme pressure conditions is determined by the load wear index (LWI). Three measurements go into determining the LWI. Imagine the test as a routine traffic light. The first measurement, the last non-seizure load (LNSL), is the highest applied load that exists when there is still lubrication between the 4 balls, or the “green light”. The load is then increased until the lubricant film no longer exists and there is metal to metal contact and the 2nd measurement, seizure region, occurs, or the “yellow light”. Finally the load is increased until catastrophic welding occurs, and the final measurement is determined, or the “red light”. Welding can be detected if any of the following are noticed:
The friction-measuring device undergoes a sharp transverse movement
Increased noise level of the motor
Smoking from the ball pot
A sudden drop in the lever arm
An average ball scar over 4mm is recorded
Using the values of these parameters, the Load-Wear Index can be calculated, which gives a numerical value to compare a grease’s ability to prevent wear at applied loads. Based on this value, one can formulate greases with different levels of extreme pressure properties.
Wear scar properties and coefficient of friction of a lubricating grease can also be determined using the 4 Ball Wear configuration. The purpose of this test is to determine the wear preventive characteristics of a lubricant. In the 4-Ball Wear test, a steel ball is rotated against three lubricated stationary steel balls under a specified load, speed, temperature and time, per ASTM D-2266 (grease) or ASTM D-4172 (oils). The better the lubricant is at preventing wear, the smaller the wear scar will be on the three stationary balls. At the conclusion of the test, the three wear scars are measured and the average is reported. The coefficient of friction is also measured throughout the 60 minute test with the average being reported at the end of the test.
4-Ball data is useful to differentiate between lubricating greases having different levels of load bearing capabilities, wear protection and friction reduction. Although these results do not necessarily correlate with real life applications, the method has become an industry standard in comparing EP, wear and frictional functionality.